Green Business
Our advanced environmental technology aims
to restore the global environment and create a healthy ecosystem.
to restore the global environment and create a healthy ecosystem.
Plasma Vortex System
Nine N’s Plasma Vortex System is an innovative eco-friendly facility that completely decomposes all types of waste within a triple-layered ultra-high-temperature plasma reactor, producing electricity from harmless synthetic gas.
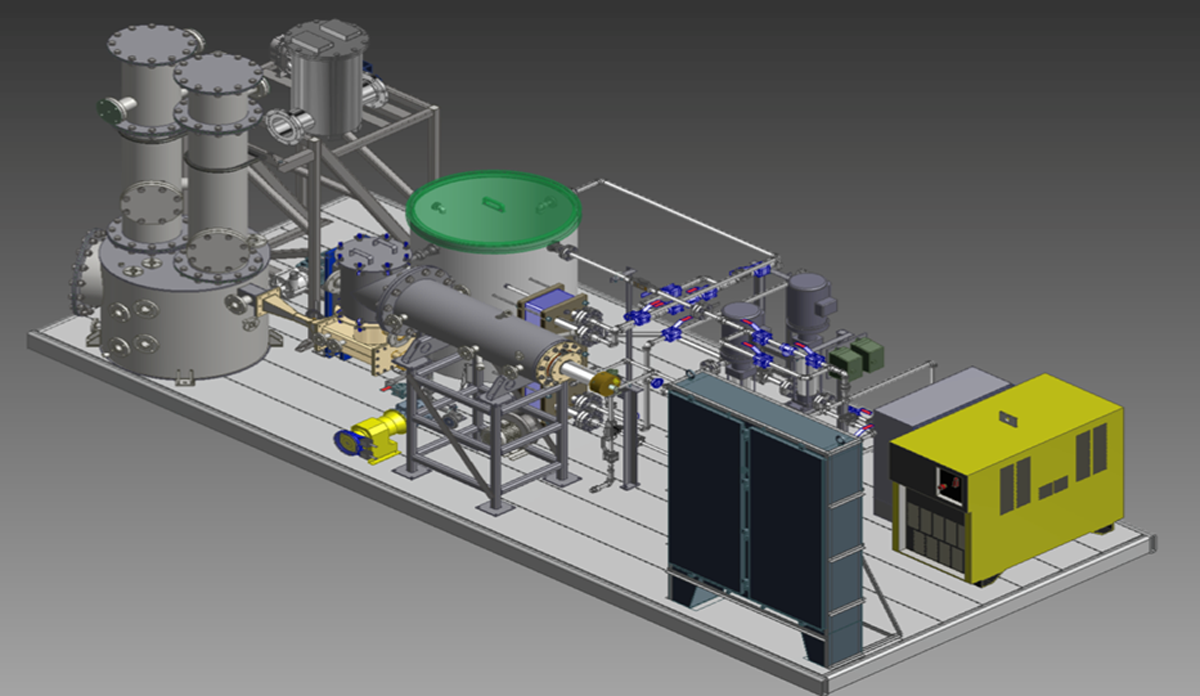
Operation System and Technologies
Other Plasma Facilities
ㆍ | Secondary pollutants and toxic materials are generated from reactors (oxidation reaction) |
ㆍ | Ex) InEnTec (the US), Plasco Energy and Alter NRG (Canada), Advanced Plasma Power (the UK), Europlasma (France), ScanArc (Norway) |
Nine N’s PVS
ㆍ | Same operation system with nuclear power plants reactors (reduction reaction) |
ㆍ | Plasmoid (black hole) within reactors disposes waste with super high temperature (up to 6,500℃) and spinning speed (40,000rpm) |
ㆍ | Plasmatron forms Hafnium and endures up to 10,000℃ |
ㆍ | Use special cooling system and water (waterdrop size: 60 nanometer) |
ㆍ | Generate energy (electricity) through cleaning system using cavitation and pulse |
ㆍ | Eco-friendly with zero hazardous material or gas emission (No chimney is required) |
Operation Process

Composition of Plasma Vortex System (PVS)

Strength of PVS
Eco-friendly
ㆍ | All kinds of waste can be disposed and free from hazardous materials. It only produces Syngas and electricity. |
ㆍ | No secondary pollutants such as dioxins, CO2, furan, etc. |
Safe
ㆍ | Easy to install and operate. No direct contact with hazardous waste. |
ㆍ | Water from cooling system protects workers against electromagnetism and radiation. |
ㆍ | Eco-friendly disposal process generates zero hazardous materials. |
ㆍ | PVS is designed to seek maximum safety adopting the same tech system used for oil and gas production. Supercomputer can conduct real time troubleshooting. |
Efficient
ㆍ | Generate 0.5~1kw electricity from 1kg of waste → Westinghouse’s system generates similar amount of electricity, but it requires high consumption of electricity for its plasma torch. |
ㆍ | Plasmatron only requires 10~20kw electricity → Requires small amount of electricity for 6 small plasma torch and control panel only. |
ㆍ | Long-term use of reactor: 30 years |
ㆍ | Recycle of residue → Final residue comes in a basalt slag type (1-3 kg per 1 ton of waste) can be recycled as construction materials |
ㆍ | Minimizing the number of operation staff ashigh performance supercomputer monitors and troubleshoot real time. |
Cost-effective
ㆍ | Low costs for facility building, operation, and maintenance |
ㆍ | Zero costs related to landfills |
ㆍ | Drastic reduction of social costs → No appeal or claim from residents of potential landfills and waste incineration plants. |
ㆍ | PVS is portable in case of natural disaster, bird flu, etc. and mobility reduces costs significantly for waste collection and transportation. |
ㆍ | Profits from electricity sale → Generate 60-120 mw electricity per day when PVS processes 5 tons of waste per hour. 97 % of the electricity can be sold while only 3% will be sent back to reactor for PVS operations. |
ㆍ | Profits from operations → Estimated annual profit: About 5.76 billion (KRW) when PVS processes 5 tons of waste per hour. (5 tons X 24 hrs X 320 days / About 150,000 (KRW) of gain per ton) |
Easy to maintain
ㆍ | No disruption during maintenance → No need to stop operations until engineer visits facility for troubleshooting → When one plasma torch is out of order, the rest will continue to function. Easy for part replacement and repair |
ㆍ | Use 2,000-3,500 hours without vortex module replacement if use cooling electrodes → 5-year warranty by cooling electrodes manufacturer |
Comparison with Other Competitors
Operator | Temperature | System | Reactor | Weakness |
---|---|---|---|---|
WestingHouseAlter NGR |
|
Cylinder Furnace |
|
|
PLASCO ENERGY |
|
Thermal Decomposition Reactor Gas Burner Furnace |
|
|
Nin N (PVS) |
|
Cylinder Reactor |
|
|
Metal Separator
Nine N’s metal separator is a state-of-the-art, eco-friendly facility that separates necessary components using electric and mechanical forces instead of traditional water or chemical treatment methods.
This technology can separate and concentrate all types of mined raw materials without the use of large amounts of water, chemicals, or reagents. High-voltage and high-frequency separation is based on differences in the electrical conductivity of separated elements, enabling the easy separation of conductors, semiconductors, and non-conductors. The process works by the interaction of electrical and mechanical forces acting on differently charged particles, altering their movement trajectory. This technology increases the metal extraction rate from slag by up to 99%.
This technology can separate and concentrate all types of mined raw materials without the use of large amounts of water, chemicals, or reagents. High-voltage and high-frequency separation is based on differences in the electrical conductivity of separated elements, enabling the easy separation of conductors, semiconductors, and non-conductors. The process works by the interaction of electrical and mechanical forces acting on differently charged particles, altering their movement trajectory. This technology increases the metal extraction rate from slag by up to 99%.